Key Advantages and Considerations of Implementing Plastic Extrusion in Your Jobs

Comprehending the Basics of Plastic Extrusion
Plastic extrusion, a staple in the production market, is a process that involves melting raw plastic material and improving it right into a continuous profile. This account, as soon as cooled down, can be reduced into preferred lengths or coiled for later use. The elegance of plastic extrusion lies in its adaptability. A large range of items, from piping to home window structures, can be generated. The process needs an extruder, a detailed maker with a heated barrel, a rotating screw, and a die at the end. The plastic product, in the form of pellets, is fed right into the extruder, where it's melted and forced through the die, taking its form. The selection of plastic and the layout of the die determine the item's features.

The Economic Benefit of Plastic Extrusion
The financial advantage of plastic extrusion lies predominantly in two areas: cost-efficient material production and helpful manufacturing speeds. With plastic extrusion, companies can create high volumes of product at a reduced expense compared to various other methods. The process boasts an impressive manufacturing speed, considerably minimizing time and further boosting its financial stability.
Cost-Effective Material Manufacturing
A substantial advantage of plastic extrusion is its exceptional cost-effectiveness. In addition, the extrusion procedure permits for a high level of precision in shaping the plastic, minimizing the requirement for expensive post-production alterations or modifications. All these elements make plastic extrusion a very economical selection for many jobs, offering an appealing equilibrium between price and efficiency.
Beneficial Production Speeds
While maintaining the cost-effectiveness of the materials, one more notable advantage of plastic extrusion lies in its rapid manufacturing rates. This mix of top quality, cost-effectiveness, and rate emphasizes the substantial financial advantage of executing plastic extrusion in various tasks.
Convenience and Personalization: The Staminas of Plastic Extrusion
One of the noticeable toughness of plastic extrusion lies in its versatility and modification possibility. These high qualities open the door to unrestricted style possibilities, offering makers the ability to tailor items to specific needs. This enhanced level of customization not just improves item capability but additionally dramatically increases item uniqueness.
Unlimited Style Possibilities
Plastic extrusion beams in its ability to supply practically limitless style opportunities. This technique supplies liberty to create intricate shapes and complex accounts, a feat difficult to attain with other construction strategies. Owing to the fluid nature of liquified plastic, the procedure is flexible sufficient to produce a diverse variety of dimensions, dimensions, and types. The plastic can be adjusted to match distinct specifications, browse around these guys permitting the manufacturing of customized geometries and meeting details customer demands. Plastic extrusion can handle a variety of plastic types, broadening its application extent. This adaptable technique, consequently, offers a broad variety of markets from building and construction to automotive, packaging to electronics, and beyond. With plastic extrusion, the style opportunities are virtually unlimited.
Boosting Item Individuality
The convenience of plastic extrusion can significantly boost product uniqueness. This procedure enables designers to explore different forms, dimensions, and shades, providing them the freedom to produce unique products that stick out out there. It is this customization that lends a distinctive identity to each item, distinguishing it from its rivals.
In enhancement to its visual benefits, the customizability of plastic extrusion likewise provides practical benefits. Designers can change the residential properties of the plastic according to the certain needs of the application, improving the item's capability. For example, they can make the plastic more versatile, a lot more resilient, or more immune to heat, depending upon what the product requires. Hence, plastic extrusion not only boosts product originality however additionally its energy and marketability.
Design Limitations in Plastic Extrusion: What You Required to Know
How can make limitations potentially impact the process of plastic extrusion? While plastic extrusion is flexible, layout restrictions can cut its benefits. Specific facility designs may not be practical because of the constraints of the extrusion procedure, possibly restricting the creation of complex accounts. The procedure is less appropriate for multi-chambered or hollow structures. Furthermore, the extrusion procedure might not constantly offer the wanted surface finish, especially for those needing high gloss or optical clarity. Material choice can additionally posture difficulties, as not all polymers are suitable for extrusion. High-temperature resistant plastics, for circumstances, may provide troubles. Recognizing these restrictions is essential for effective application of plastic extrusion in your jobs. plastic extrusion.
Assessing the Environmental Effect of Plastic Extrusion
While recognizing layout constraints is a substantial element of plastic extrusion, it is just as important to consider its ecological effects. The procedure of plastic extrusion includes melting plastic materials, potentially releasing harmful gases right into the setting. Additionally, the resulting products are typically non-biodegradable, adding to land fill waste. Nonetheless, improvements in modern technology have actually permitted more environmentally-friendly techniques. Making use of recycled plastic products in the extrusion process can lower environmental impact. In addition, creating naturally degradable plastic alternatives can aid alleviate waste issues. Evaluating these ecological factors is essential when applying plastic extrusion jobs, making sure a balance in between performance, cost-effectiveness, read the full info here and environmental duty.
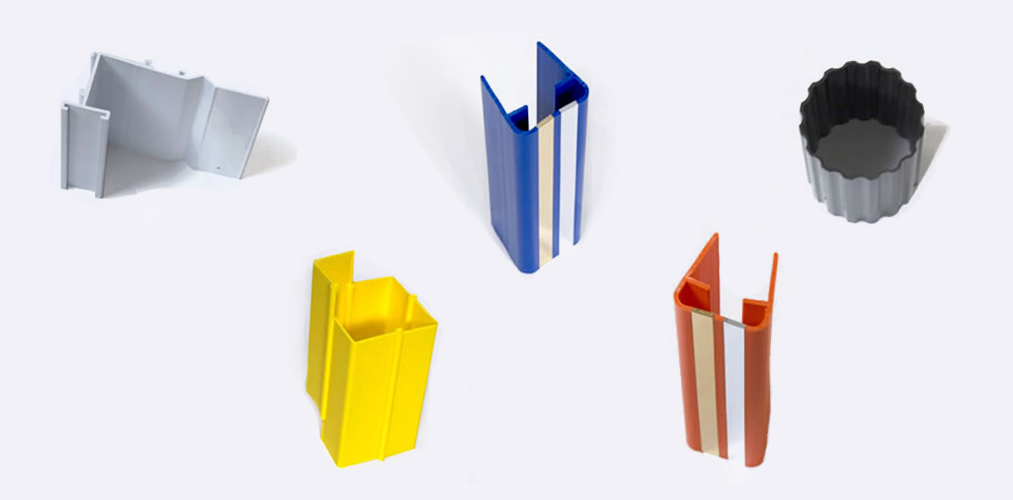
Study: Successful Projects Using Plastic Extrusion
Success tales in the area of plastic extrusion are plentiful, showing both the versatility and efficiency of this manufacturing process. One noteworthy example is the development of PVC pipelines used in contemporary plumbing. This process involves melting plastic and forming it right into a continuous tube, offering significant price and resilience advantages. An additional successful instance is the manufacturing of plastic movie for packaging and agriculture. Via extrusion, manufacturers can generate very personalized, slim, and durable movies. Automotive markets likewise benefit, utilizing extruded plastic for parts like trim or seals, improving car longevity. These circumstances highlight plastic extrusion's critical role in numerous fields, vouching for its versatility, cost-effectiveness, and trustworthy outcome.
Verdict
Finally, plastic extrusion provides a reliable and cost-effective approach for creating complicated shapes with marginal waste. While it supplies numerous advantages such as cost-effectiveness and flexibility, it's crucial to think about potential style constraints and environmental results. Executing recycled or eco-friendly products can minimize these problems, boosting sustainability. Incorporating plastic extrusion into tasks can lead to successful end results, as evidenced by various study.
Plastic extrusion, a staple in the manufacturing sector, is a procedure that involves melting raw plastic material and improving it right into a continuous profile. Plastic extrusion can deal with a range of plastic kinds, increasing its application scope.How can develop restrictions potentially impact the process of plastic additional reading extrusion? The procedure of plastic extrusion entails melting plastic products, possibly releasing dangerous gases right into the setting. Making use of recycled plastic products in the extrusion procedure can minimize ecological effect.
Comments on “Plastic extrusion for optimized, scalable manufacturing solutions”